Accuracy Analysis of the workpiece when turning shaft
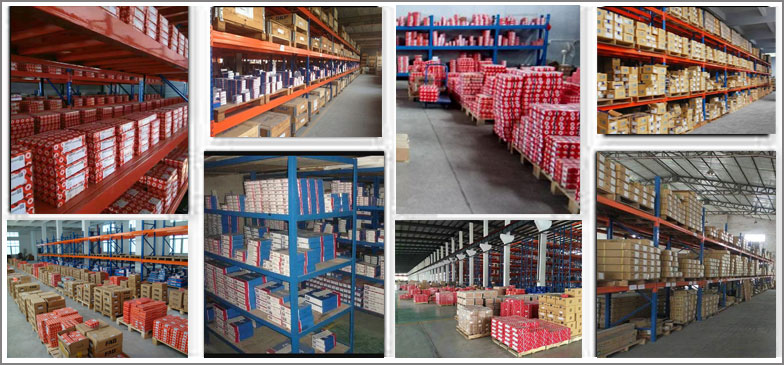
Most favorable price :
sales@hellerbearings.com We can provide free samples . Please contact Email for any inquiries
Shaft parts in the turning process , will encounter accuracy and surface roughness below standard and other issues. Depending on the process of turning when , for analysis.
First, the dimensional accuracy is mainly the reason for their solutions
1 Since the operator is not careful, measured when children go awry , or dial the wrong and improper use of it in the measurement , to carefully and correctly use the dial is very important to handle the dial on the carriage , the various types of lathes dial is not the same , each small grid of available dial the following formula: a grid -scale transfer carriage screw turning movement distance = distance / dial engraved lines in total cell number (mm) know each after the grid scale values ??, but also pay attention to when using because the gap between the screw and nut , although sometimes dial rotates , but will not necessarily turning move , so after turning it completes a gap move . So when in use, the number of cells if the scale turned too far , never allowing only rewind a few cells, but to reverse after a turn , and then re- align the scale.
2 measuring themselves there before being put to use measuring tools, must be carefully checked and adjusted the error or , to put a positive use.
3 due to temperature changes, changes in the size of the workpiece during cutting , the chip is deformed , each individual molecules to move between each of the chips , which occurs when the friction generated by moving a lot of heat. Further, since the chip and the front friction tools , turning tools and the workpiece rear surface friction also generates heat, which directly affect up to the tool and the workpiece . Of course , the heat is highest chips ( about 75 percent ) , followed by turning ( about 20% ) and the workpiece ( about 4% , and 1% in air) . After heating the workpiece diameter is increased ( approximately 0.01 to 0.05 mm , cast steel material change than large ) , diameter shrinkage after cooling , resulting in a waste. When it does not go very high workpiece temperature measurement . If a certain amount to the side when turning pouring enough cutting fluid, not the workpiece temperature ; followed by separate coarse and fine cars approach.
Killing four . Rough rough enough in itself bent over the whole no straightening , and a central hole he missed other reasons .
Second, the geometry of the accuracy and precision of mainly the mutual position of the main reasons
Cause of an ellipse . Occurred
a. ellipticity shaft journal is directly reflected in the work up, if the sliding bearing , the load when the same size and orientation , the main journal is pressed under load at a predetermined position on the bearing surface ( the spindle and a gap between the bearing ) . When the spindle is rotated 90 °, the change in the center position of the spindle , the spindle so that the center position in the course of two rotation , the tools, the tool back to eat the amount of change , leaving the workpiece ellipticity. Ovality no effect on the bearing bore of the workpiece .
b. blank margin uneven , with the gap between the shaft and bearing , in the process of cutting back the amount of change in eating knife .
c. around the center hole does not match ( two center hole at an angle with the workpiece center ) , the center hole only come into contact with the top side, causing uneven wear from oval axial movement
d. former top swing.
Generated bus is not straight ( sterile curved , convex, saddle -shaped ) and taper Cause 2 .
a. lathe spindle center rail and the mutual position is not correct , especially in the horizontal . Such as rail bent, convex or concave workpiece , not parallel to the centerline of the spindle guide cone and other produce .
b. around the top centerline and bed rails are not parallel , resulting taper.
c. Due to the workpiece temperature, causes the shaft to bend . For example, when the heavy long axis lathe , the temperature rises to a certain time , the workpiece will be extended, but the distance between centers remains unchanged, since the results of the work can not be elongated in the longitudinal direction of the bend . Therefore, when the long axis of the car , minimizing temperature , but also the top must often look back .
d. internal stress of the workpiece affected. There is often the internal stress of the workpiece , the cutting process , the plastic deformation of the surface layer , will produce stress , this stress state of equilibrium in the interior of the workpiece , to maintain a certain shape of workpiece , but when the workpiece from the jig or unloading lathe the next , it is necessary deformation. solve this problem , the general aging treatment methods. 3 reasons runout caused sharp pulsating in the preceding paragraph ; center hole is not round or chips and other dirt ; course there ovality surface can cause runout .
Third, the main reason is mainly the surface roughness
1 . Less rigid lathe carriage as iron loose plugs , transmission disequilibrium caused by the vibration of course , lathe installation can cause unstable vibration , the vibration caused by the surface roughness is reduced.
(2) lack of rigidity caused by vibration so as turning crude selection Arbor, reduce turning out of a length ; less rigid workpiece can cause vibration , so when you want to apply the elongate shaft turning center rack, or a folder with a top instead of two top fixture . 3 lathe cutting part geometry is not correct according to the workpiece material can be a reasonable choice of cutting characteristics suitable cutting angle to reduce the surface roughness.
4 Because BUE generated so that the surface roughness is reduced BUE very strong, cutting due BUE participation so that the surface appears nap or a road plan grooves phenomenon should try to avoid turning produced . Combination of the foregoing analysis, the processing should be done early to know early prevention , the problem is nipped in the bud , to improve the accuracy of the workpiece , meet the design requirements .
234407BM 234706BM 234406BM 517/2860V/YA 5610/2500 517/1720X1V 527/1181M 510/1180M 517/930 510/670 590/560 510/500 52780 59080 517/368M 51760U 517/238 6207-2ZN 6206-2ZN 6205-2ZN 6204-2ZN 6203-RZ 6203-2ZN 6202N 6202-2ZN 6201-2ZN 6200ZZ 6200-2ZN 62/32-ZN 62/32-Z 62/32N 62/32-2Z 62/32-2RZ 62/32-2RS 62/28-2RZ 62/22-2RZ 61996 61992 61988 61984